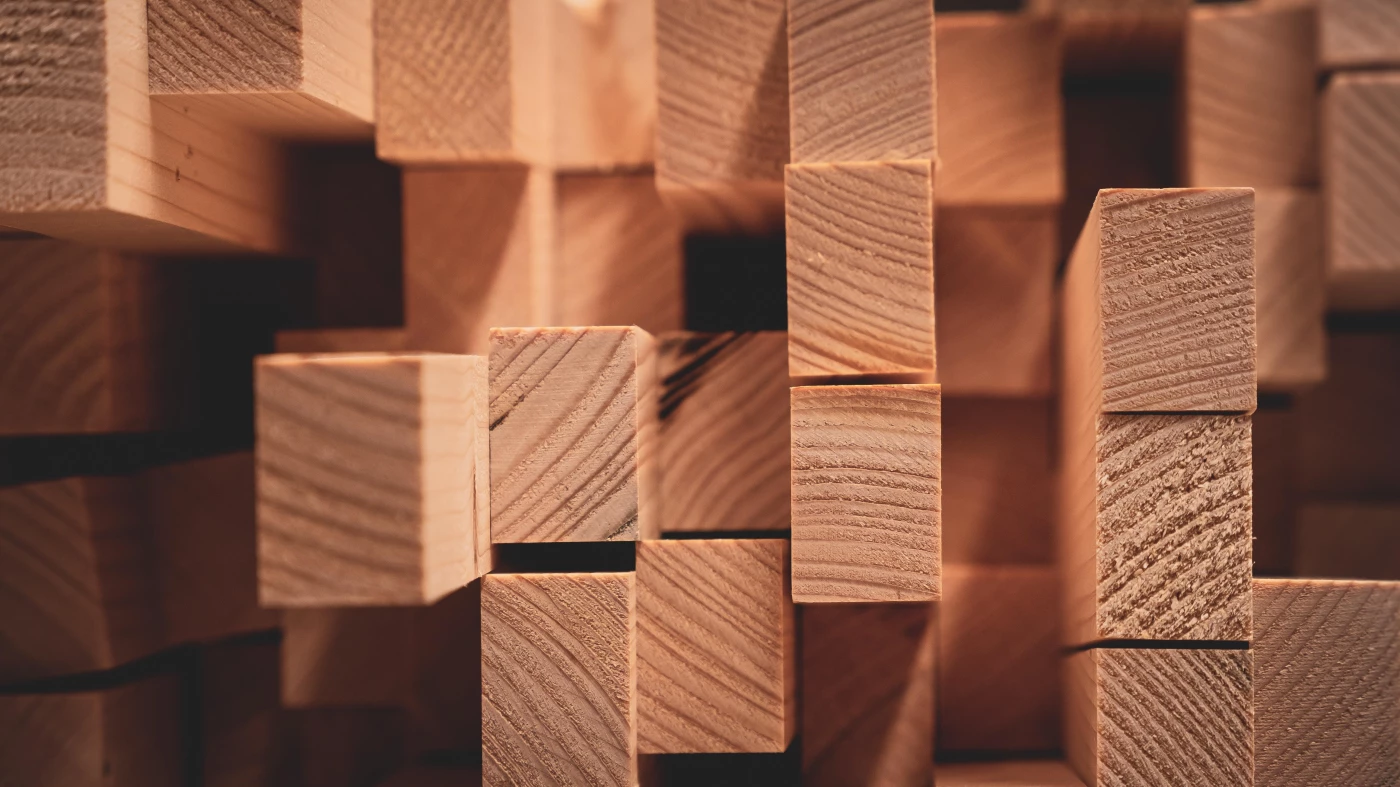
27. 1. 2025
Industrial wooden buildings attract attention
The industrial real estate sector is responding to growing pressure for sustainability and environmental responsibility by making greater use of eco-friendly materials. As a result, industrial timber buildings are becoming fashionable. They represent one of the most significant trends in contemporary commercial development. While this type of construction has already proven its viability in Western Europe, especially in German-speaking countries, the Czech market is only just discovering it.
"Wood buildings can serve as an environmentally friendly alternative to conventional concrete or steel warehouses, as wood contributes to reducing the operator’s carbon footprint. At the same time, timber buildings can be built faster than traditional halls. This offers a significant advantage in the logistics sector where time plays a key role," says Desanka Timkovska of Colliers, adding that pilot projects (such as smaller warehouses or distribution centres built at least partly from wood) are already being developed in the Czech Republic. Panattoni, the first company on the Czech industrial development market to receive a positive opinion for the use of wooden trusses and roof trusses in the construction of large-scale industrial halls for production and logistics, is planning the first major project on the local market. This is Panattoni Park Pilsen West III in Úherce: 14 kilometres west of Pilsen. The new building will offer more than 40,000 m² of leasable space.
Benefits
The main advantage of timber buildings is their significantly lower carbon footprint compared to conventional buildings. As a building material, wood actively absorbs CO2 from the atmosphere during its growth and this carbon remains bound in the structure throughout its lifetime. An industrial timber building can therefore save up to 50% of CO2 emissions compared to a similar building made of concrete and steel. With proper forest management, it is also a fully renewable resource. In addition, the Czech Republic is the largest exporter of raw timber in the EU and its greater domestic use would support the development of higher value-added businesses.
Economics is another important factor. The initial investment in an industrial timber building can be 10-15% higher than for conventional buildings, mainly due to more sophisticated fire protection solutions and the higher price of quality structural timber. However, these costs are partly offset by faster construction and therefore an earlier return on investment. At the same time, a typical industrial timber building can be completed 20-30% faster than a similar building made of concrete and steel. This is because timber structures can be prefabricated in a factory and then quickly assembled on site; reducing construction time and minimising disruption to the surrounding area. It also leads to greater precision and quality of construction because the prefabricated parts are manufactured in a controlled environment.
Experience with industrial timber buildings to date has yielded a number of positive findings. Users highlight a significantly more pleasant working environment and improved thermal comfort with a positive impact on employee productivity. Building maintenance is comparable to that for conventional buildings, which calms investors' initial fears of potentially higher operating costs. Another advantage is lower energy consumption for building operations due to the timber structures’ better thermal insulation properties. And acoustics also outperform those of conventional steel halls.
Disadvantages
However, industrial timber buildings also face several significant challenges. First and foremost are the more stringent fire regulations and the associated sophisticated, and often costly, fire protection solutions. Chemical impregnation of timber, the installation of powerful sprinkler systems and the use of special fire-resistant cladding are standard.
Another technical challenge is protection against moisture and biological pests. Modern industrial timber buildings use a combination of structural protection (proper detailing and ventilation) and chemical impregnation. The lifetime of such protected structures is around 50 years with proper maintenance, which is comparable to conventional buildings. However, developers must take into account that not all types of industrial sites are suitable for timber buildings. For example, sites with high humidity or aggressive environments require special treatments and protective measures.
Legislative regulations are another issue altogether. Today, for example, the height of wooden buildings in the Czech Republic cannot exceed 12 metres, which corresponds to between four and five storeys. Currently, lawmakers are gradually revising the regulatory framework for construction of industrial wooden buildings and specialised norms and standards are being drafted. Sustainability certification systems such as LEED or BREEAM also play an important role.
Application
"In practice, timber buildings are best suited for light logistics, distribution centres and environmentally controlled warehouses. On the other hand, they are less suitable for heavy industry or facilities with high demands for chemical resistance," says Desanka Timkovska. For example, in the case of heavy industry or storage of heavy materials, the load-bearing capacity of wooden structures may be insufficient. Also, in areas with a high risk of fire or extreme humidity, the use of timber can be problematic.
The future
In the long term, industrial timber buildings represent a promising direction for building design. With the gradual improvement of technologies, we can expect their wider adoption on the Czech market. Tightening environmental requirements, technological progress, economic aspects and investor confidence will play a crucial role in local choice evolution.