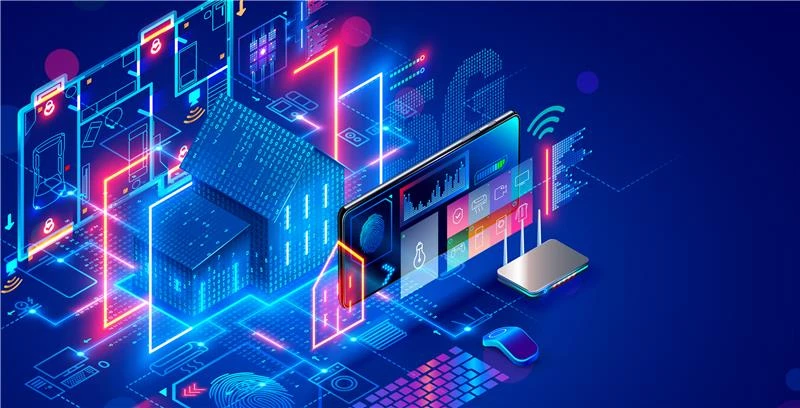
13. 11. 2024
Building automation - a sustainability helper, not a band-aid
So what about those vaunted technologies? How do we define them and how do we use them in buildings so that they make sense? Today, let's focus on one of the measures mentioned in the case study collection: automation.
Building automation by the shovelful
Building automation is also known by the acronyms BMS (Building Management System) and MaR (Measurement and Regulation). It provides automated management and control of all the technologies that ensure a healthy indoor environment, i.e., heating, cooling, lighting, shading and controlled ventilation with heat recovery. In addition to monitoring and maintaining the quality of the indoor environment, building automation also oversees the monitoring of energy consumption and therefore energy, i.e., environmental, performance.
From this description of the use of automation, we can already quickly see some benefits in all three areas of ESG. In area E, we have the possibility to reduce energy consumption, to make energy use more efficient in individual consumption types and, last but not least, to reduce energy consumption on the basis of energy volumes.
In area S, the biggest benefit of properly designed automation is the aforementioned high-quality internal environment. This translates in the office space into lower rates of employee illness and therefore absenteeism, a higher level of attention and work efficiency, and also, perhaps harder to grasp, overall mental well-being. Automation also eliminates operational 'oversights' by individuals, such as windows left open for long periods of time when the heating is on full blast, or blinds left drawn when employees can benefit from natural daylight. This helps to maintain objectively correct values for the factors that affect our indoor well-being.
Last but not least, it facilitates the automation of control, i.e., area G. Thanks to the technologies in place, the user receives the data needed for correctly setting an operational strategy, its eventual implementation and now, in the case of some companies, so-called non-financial reporting (according to the CSRD and its ESRS standards).
So are these technologies THE solution to our problems? Yes, but never as a first step and certainly not as the only step.
The sustainability hierarchy
Sustainability in buildings is not really a simple topic; even if we simplify it to the area of energy efficiency. Yet there is a relatively simple lesson to be learned that will not let you down in your decision making. Minimise consumption and cover what you have left over with renewables. The first step is that I design the building, i.e. our main appliance, so that it needs as little energy as possible. I have to assess the structure: how it lets light in and with that light heat, and also air, and how it dissipates heat. The building’s internal layout, the materials chosen and other aspects also play a role. In the second step, I address what the building will not take care of on its own, i.e., passively. This means where we need to help it actively with heating, cooling, water heating, light or air supply, technology comes first - the building's Technical Building Systems (BTS). These need a certain amount of energy to run, which should preferably be from emission-free sources.
Does this also apply to existing older buildings? Absolutely! The starting position will be more difficult, but the process is the same. Once you've treated this baseline, our MaR and BMS acronyms come into play.
Do you have a BMS? Could I see it?
All technologies, such as air conditioning units, heating and cooling sources (gas boilers, heat pumps, chillers, air conditioners ...), and lighting or shading are connected to programmable logic controllers (PLCs) located in MaR cabinets. In addition to these, various sensors for the measurement of operating parameters or indoor air quality (CO2, relative humidity, temperature); local control elements, e.g., for setting the required temperature correction; etc. are connected to these PLCs. Let me make one more simplification: namely procedural. After connecting the PLC by cable or wirelessly, I program and record the control algorithm. Multiple PLCs connected together give me a BMS where I collect data and control the individual HVAC systems using an ideally pleasant graphic interface. Other important building systems such as fire, security or attendance systems are usually also connected to the BMS, but that's a story for another time...
So when does automation make sense and what does it not deliver true value?
Generally speaking, automation makes sense in larger building units where one has to monitor several operational parameters. Thanks to systems’ interconnectedness, the building can react to external changes such as weather fluctuations, as well as to internal stimuli such as the individual comfort of the various tenants in office buildings, industrial companies’ specific operating conditions and production requirements or the high stability of hospital operations, etc. It is also the only tool that provides a comprehensive overview of how technologies are operating and the associated costs. In addition, today's solutions enable the integration and efficient control of, for example, rooftop photovoltaics in combination with battery energy storage or the connection and control of electric vehicle charging. This is all done in such a way that energy consumption is distributed automatically and efficiently.
However, a prerequisite for benefiting from these systems is a facility management equipped with in-depth knowledge and also data analytics capabilities. Such management must be able to evaluate complex, large volumes of information; ideally, both in real time and for long-term planning.
How to start properly
- Remember the hierarchy of building needs. Automation will not save poorly configured passive building elements, nor will it eliminate emissions from the operation of poorly chosen energy sources. If you are building a new building, start with the right design and energy model. In the case of retrofits, also technically assess existing passive and active elements.
- Avoid deploying automation without knowing why you need it. For some tasks, simple calculations without complex IT will suffice; for example, calculating the carbon footprint of operational energy.
- Get your prioritisation right. Financial savings or emissions savings are definitely among them. But performance and human health may call for prioritising slightly different systems and values. What are the priorities in your ESG strategy?
- Measure for the long term and evaluate.
- Carefully consider the solution and vendor selection based on the nature of the building, the HVAC and other systems used, and your strategy for working with the data.
Interested in more details on this topic? Feel free to contact our ESG expert for a free consultation.